Mining operations present some of the most challenging and hazardous work environments across all industries. From underground excavation sites to open-pit facilities, workers face daily risks that demand proactive safety measures and comprehensive planning. Developing and implementing robust workplace safety plans is not just a regulatory requirement but a fundamental responsibility that protects lives, preserves operational continuity, and safeguards business sustainability.
Blog
Our BLOG focuses on current safety and health topics providing readers with relevant information and viable solutions for addressing safety concerns. Visit us using your favorite social media platform to contribute to the BLOG or contact us to ask a safety and health-related question.
Do you want to be the first to see our most recent BLOG? Subscribe and we’ll make sure you don’t miss it!
Sow Safety Early: Why You Need an Agriculture Workplace Safety Plan
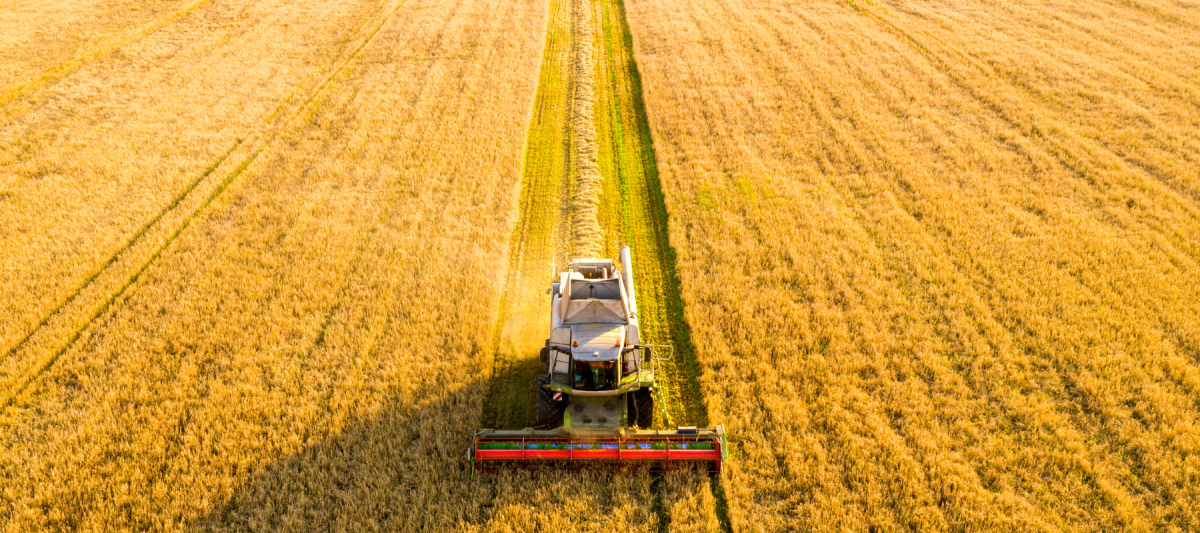
Agriculture stands as the backbone of America's economy, feeding millions and supporting countless communities across the nation. Yet, while not often talked about, agriculture ranks as the most dangerous profession in the United States, with a fatality rate seven times higher than all other industries combined. This alarming statistic underscores the urgent need for comprehensive workplace safety plans that can mean the difference between life and death for agricultural workers.
Essential Guide to Workplace Lead Exposure Prevention
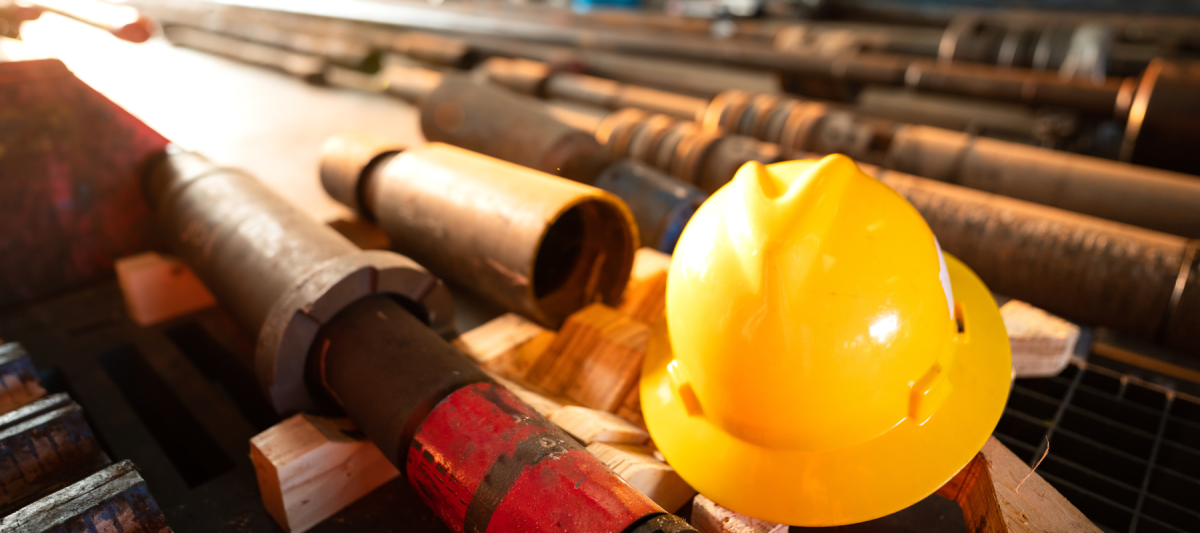
Construction workers face numerous safety hazards daily, but lead exposure remains one of the most dangerous and underestimated threats in the industry. Lead poisoning in construction affects thousands of workers annually, making lead safety training and awareness critical for protecting workforce health and ensuring OSHA compliance.
Why Investing in Construction Safety Consultation is Good Business
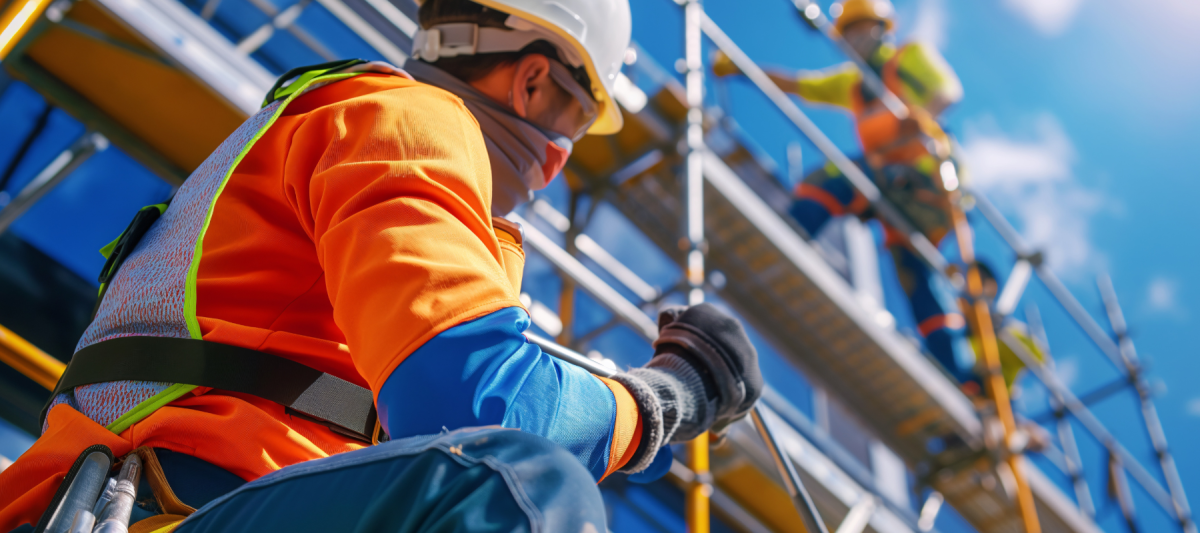
In today's competitive construction industry, savvy business leaders understand that workplace safety isn't just about compliance—it's a strategic investment that delivers measurable returns. When construction companies partner with specialized safety consultants like Northwest Safety & Risk Services, they position themselves for both immediate operational benefits and long-term competitive advantages. Here's why making safety consultation a priority makes sound business sense.
Protecting Your Most Valuable Asset: The Comprehensive Guide to Workplace Safety Programs
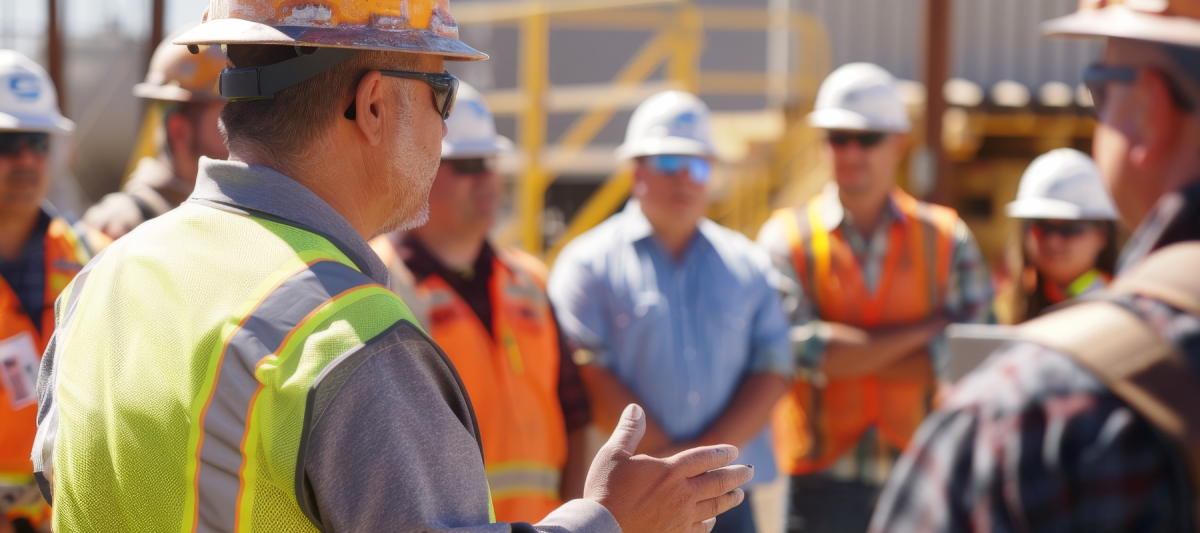
At Northwest Safety & Risk Services, we understand that workplace safety is more than a regulatory requirement—it's a critical investment in your organization's most important resource: your employees. Our years of experience have consistently demonstrated that a well-crafted safety program is the cornerstone of a successful, thriving business.
Exploring the Training Courses: Why They Are Valuable and Unique
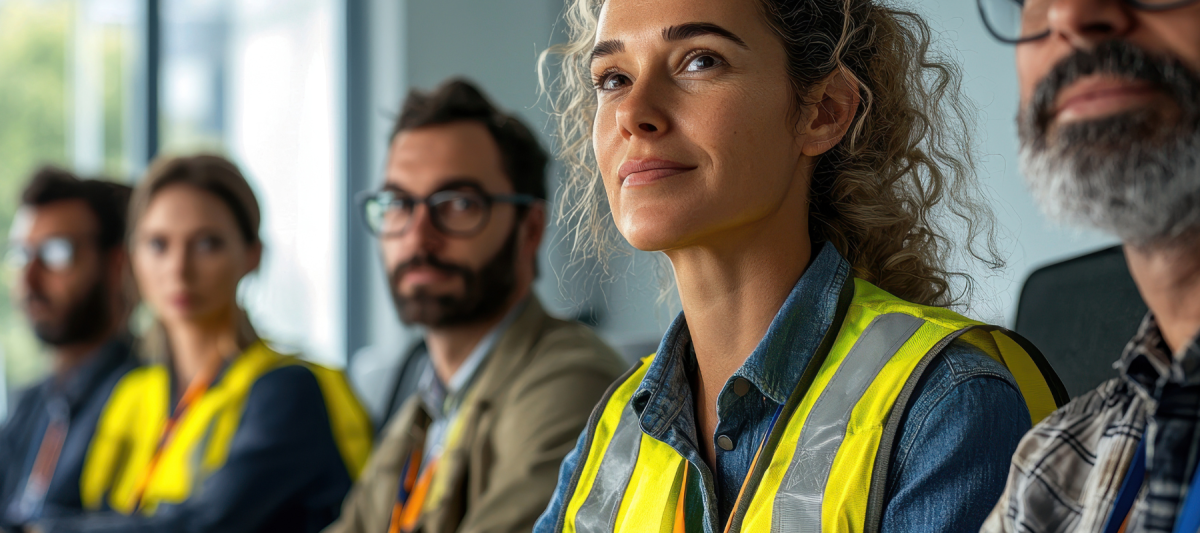
In today’s fast-paced and highly regulated work environments, safety training is more important than ever. With the need to reduce workplace accidents, ensure employee well-being, and comply with various safety regulations, companies are increasingly turning to specialized training programs to equip their teams with the necessary knowledge and skills.
Cold Stress: Protecting Workers in Winter Workplace Safety
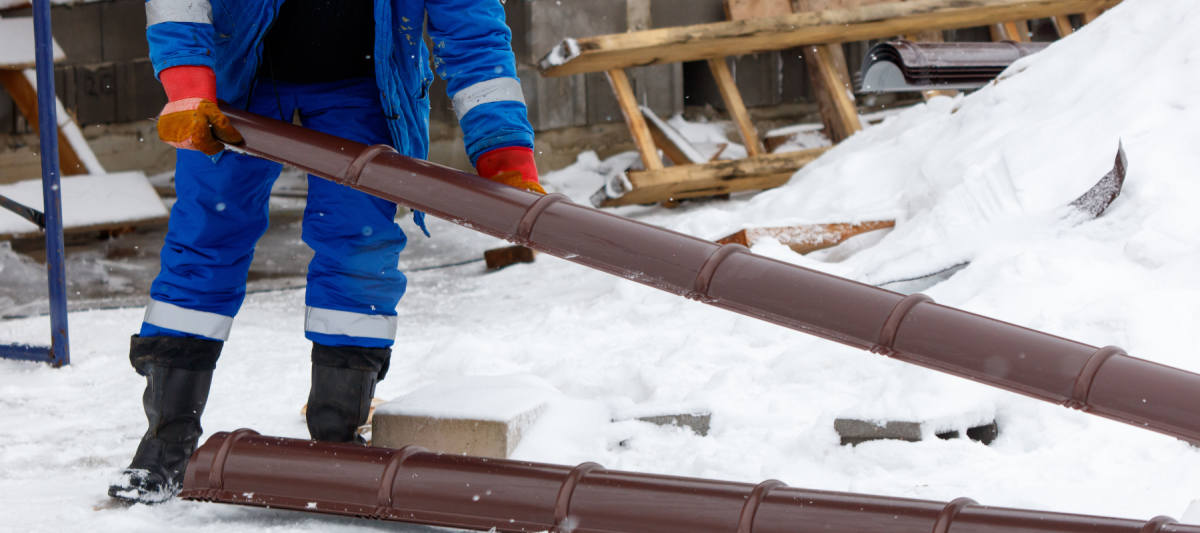
Understanding Cold Stress: A Critical Workplace Hazard
Winter brings unique challenges to workplace safety, with cold stress emerging as a critical concern for workers across various industries. Cold stress occurs when the body cannot maintain its normal temperature, causing internal temperatures to drop and potentially leading to serious health complications.
OSHA 10 vs 30: Which Construction Safety Training Is Right for You?
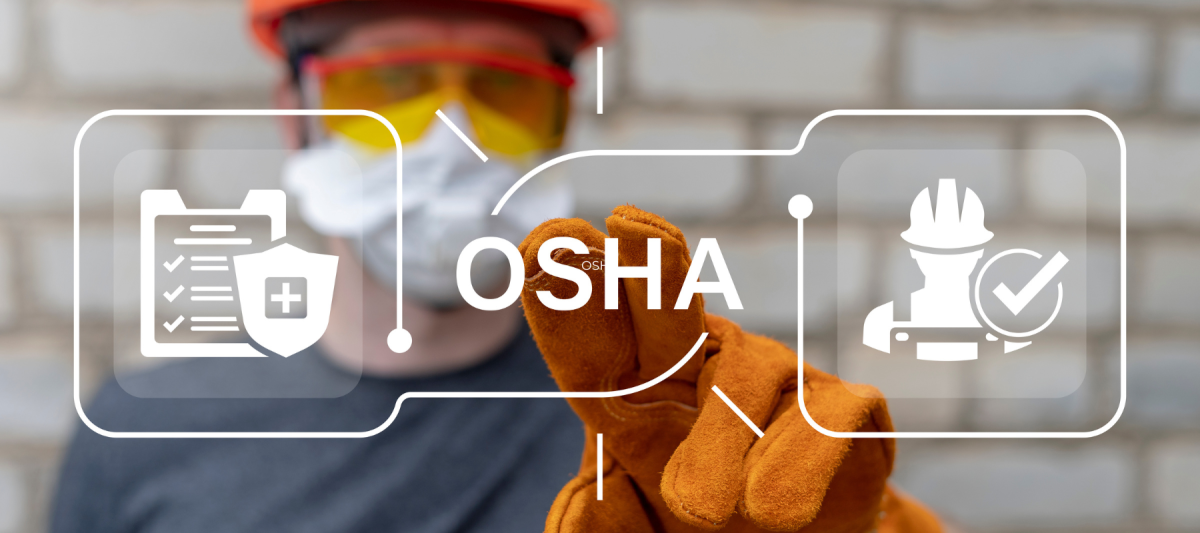
In the fast-paced world of construction, safety isn't just a box to check—it's a fundamental requirement that protects lives and livelihoods. Two of the most recognized safety training programs in the industry are OSHA 10-Hour and OSHA 30-Hour courses (both of which are offered by Northwest Safety & Risk Services). But what sets them apart, and which one do you need? Let's dive deep into these essential training programs.
Winter Weather Workplace Safety: Preparing Your Team for Cold Weather Hazards
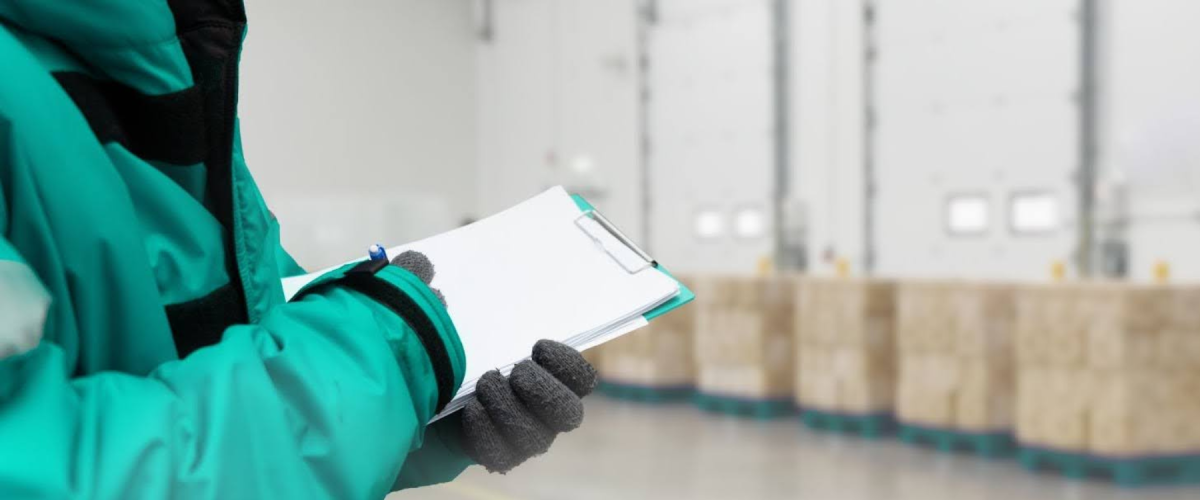
As the crisp autumn air gives way to winter's chill, workplaces across the country face a critical transition period. With winter approaching, now is the time to ensure your workplace isn't just surviving winter conditions but thriving through them with proper preparation and training.
First Aid Training: When Minutes Matter in the Modern Workplace
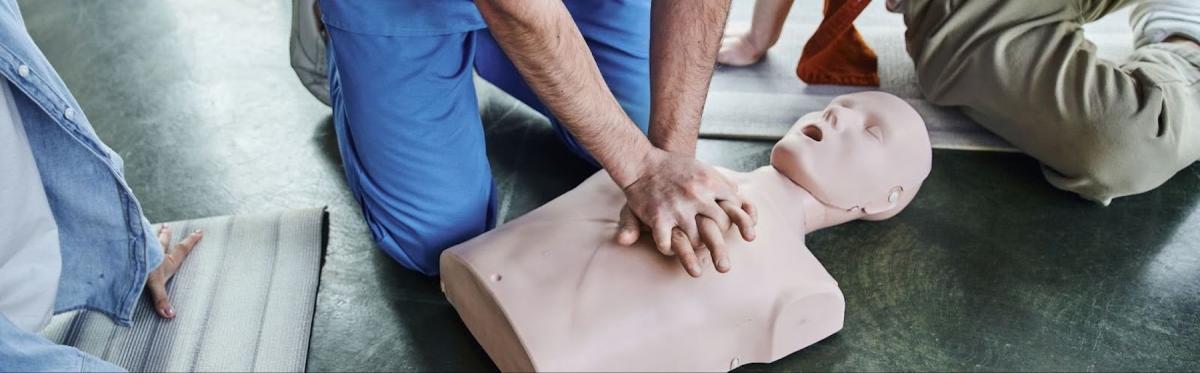
Picture this: a colleague suddenly clutches their chest in the break room. An employee cuts themselves badly while working in the warehouse. Or a customer slips and hits their head in your retail store.
In these critical moments, the difference between a close call and a tragedy often comes down to one thing: having properly trained staff who can respond immediately.