In the quiet hours before students fill the hallways, school maintenance workers and custodians are already hard at work, ensuring our educational facilities are clean, functional, and safe. Yet beneath the surface of these seemingly routine tasks lies a critical responsibility that many don't consider: protecting our school communities from hidden environmental hazards, particularly asbestos.
Blog
Our BLOG focuses on current safety and health topics providing readers with relevant information and viable solutions for addressing safety concerns. Visit us using your favorite social media platform to contribute to the BLOG or contact us to ask a safety and health-related question.
Do you want to be the first to see our most recent BLOG? Subscribe and we’ll make sure you don’t miss it!
Mental Health and Workplace Safety: An Overlooked Connection
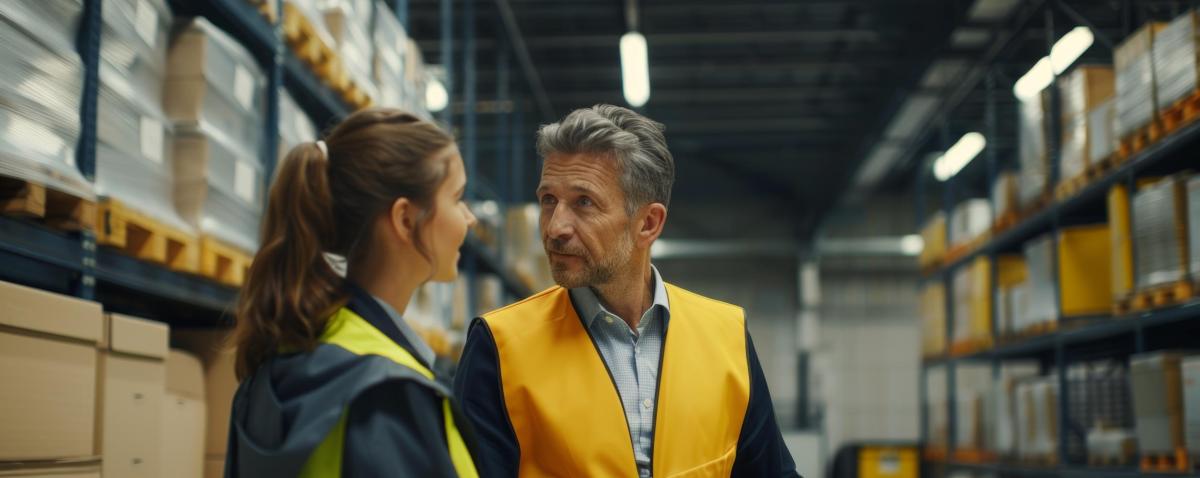
In the realm of workplace safety, physical hazards often take center stage. Hard hats, safety goggles, and proper lifting techniques are commonplace in discussions about keeping employees safe. However, a critical aspect that's frequently overlooked is the impact of mental health on overall workplace safety.
Legal Compliance and Workplace Safety Measurement: Navigating Regulatory Requirements

Workplace safety isn't just about protecting employees—it's a legal imperative. For businesses across industries, navigating the complex landscape of safety regulations can be daunting. At Northwest Safety & Risk Services, we're committed to helping organizations not only comply with legal requirements but also foster a culture of safety that goes beyond mere checkbox compliance.
Cultivating a Positive Safety Culture: Leadership’s Role in Measurement and Improvement
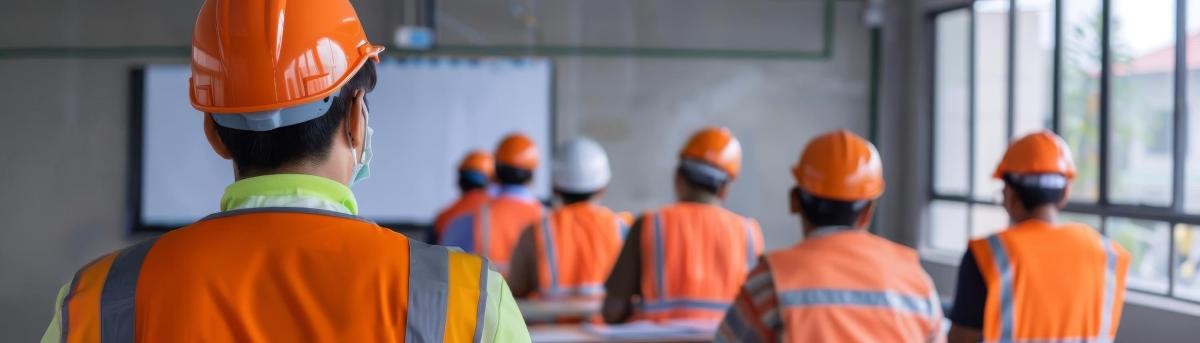
In the workplace, safety is not just a priority—it's a fundamental value that underpins every successful organization. At Northwest Safety & Risk Services, we understand that cultivating a positive safety culture is crucial for protecting your most valuable asset: your employees. But how can leadership effectively measure and improve safety culture?
Let's explore this critical topic in depth.
Building a Culture of Safety: Why Construction Training Matters More Than Ever
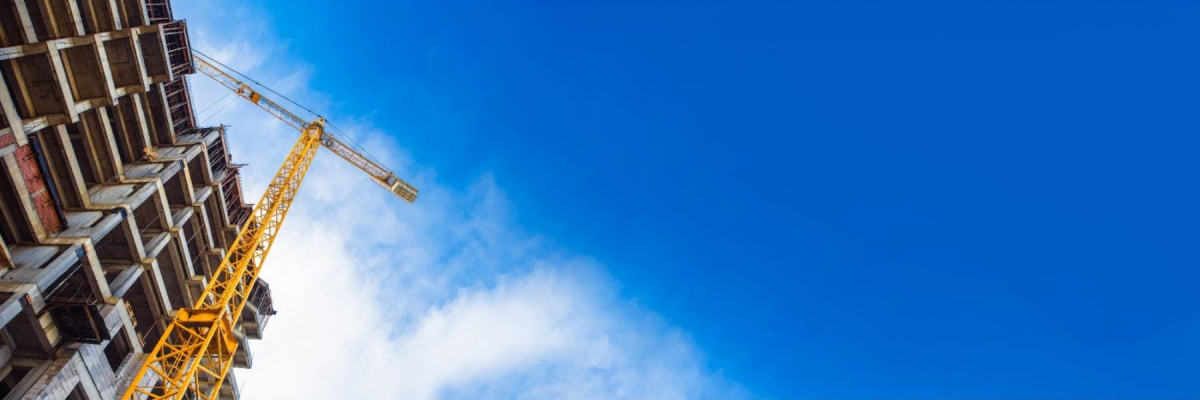
Safety isn't just a checkbox in the world of construction—it's the cornerstone of successful project execution and worker well-being. As we enter 2025, the construction industry faces evolving challenges and increasingly complex safety requirements, which is why comprehensive safety training has become vital.
Your Workplace Safety: Industry Standards and Best Practices
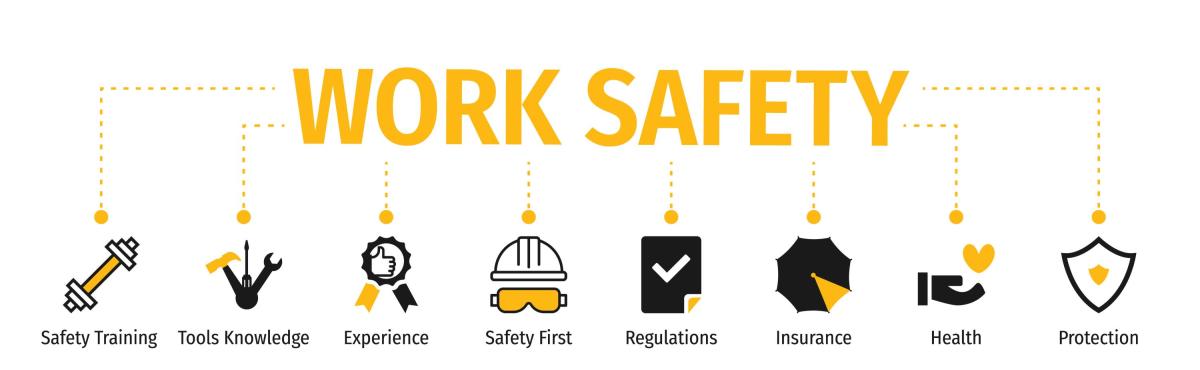
In today's rapidly evolving business landscape, workplace safety has become more critical than ever. As organizations strive to protect their most valuable asset—their employees—the importance of benchmarking against industry standards and adopting best practices cannot be overstated.
This comprehensive guide will explore how your business can leverage industry standards, comparative analysis, and emerging best practices to create a safer, more productive work environment.
Embracing Technology for Enhanced Workplace Safety Measurement
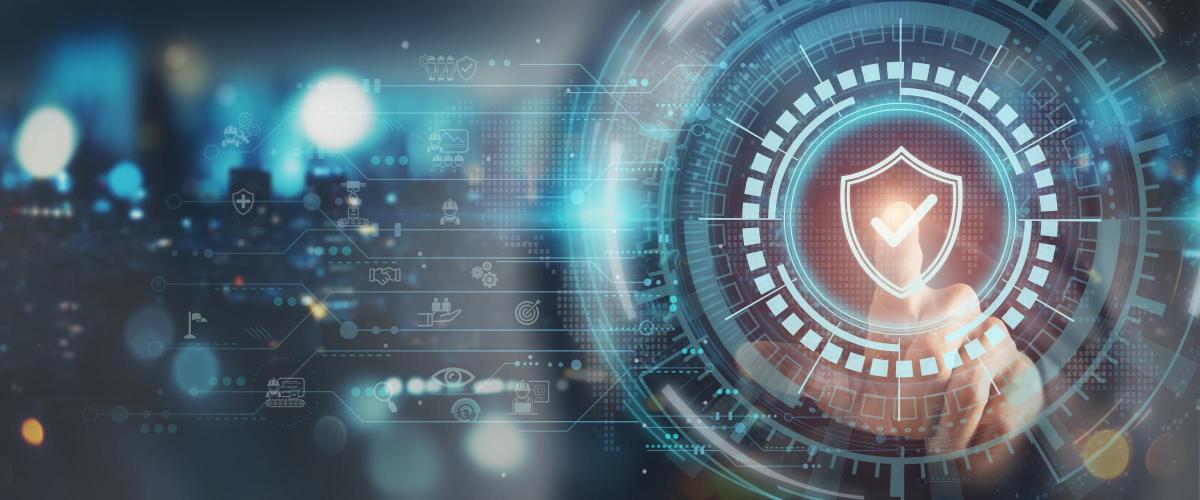
In the ever-evolving landscape of workplace safety, technological advancements have revolutionized the way we measure and ensure the well-being of employees. From real-time monitoring to predictive analytics, technology has become an indispensable tool in creating safer work environments.
Key Metrics for Evaluating Workplace Safety Performance
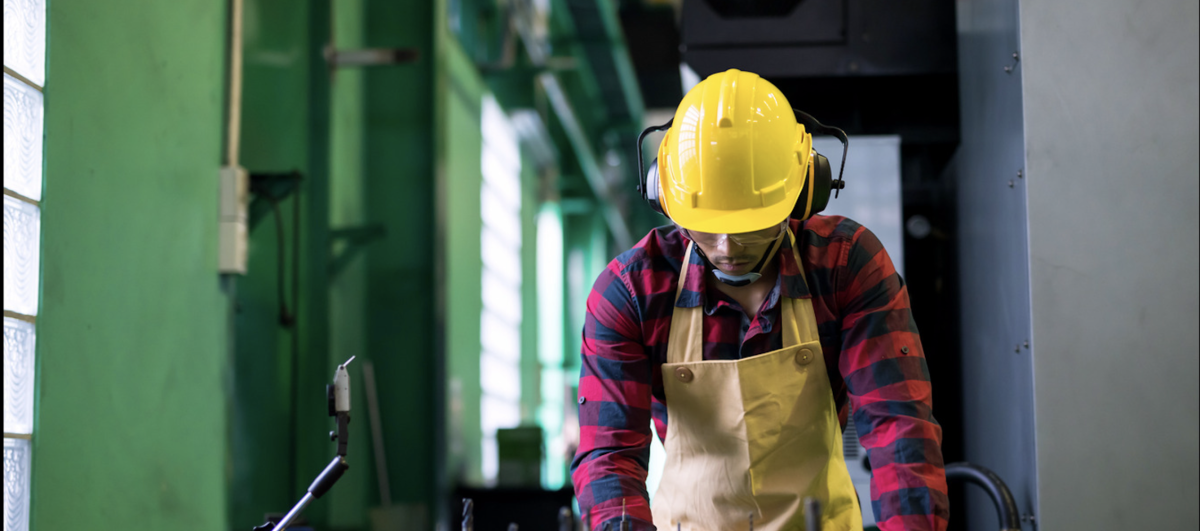
Measuring and monitoring workplace safety is crucial for any organization that values the health and well-being of its employees. However, determining the right workplace safety metrics to assess safety performance can be challenging.
Navigating Safety Challenges in the Healthcare Industry
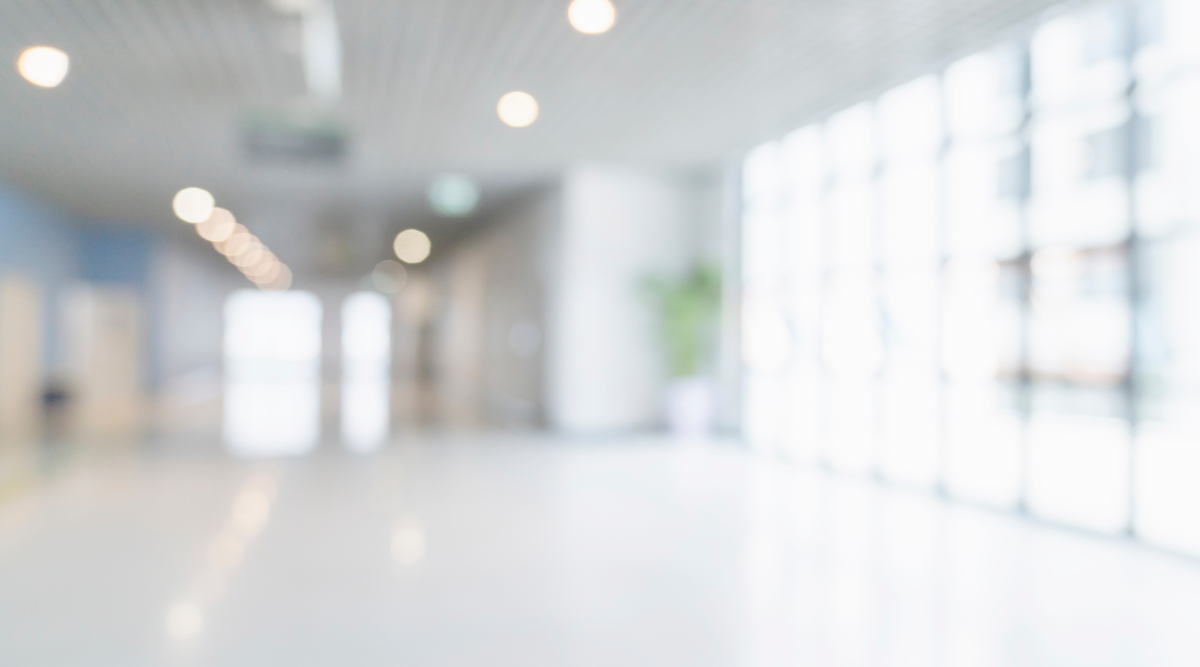
Working in healthcare comes with unique risks and hazards. Hospitals, clinics, and other medical facilities can be high-stress environments that pose a variety of safety challenges for both healthcare professionals and patients. Developing comprehensive safety protocols and training staff on best practices is essential for healthcare organizations. This blog post will explore some of the key health and safety issues faced by the healthcare industry and provide guidance on mitigating risks.