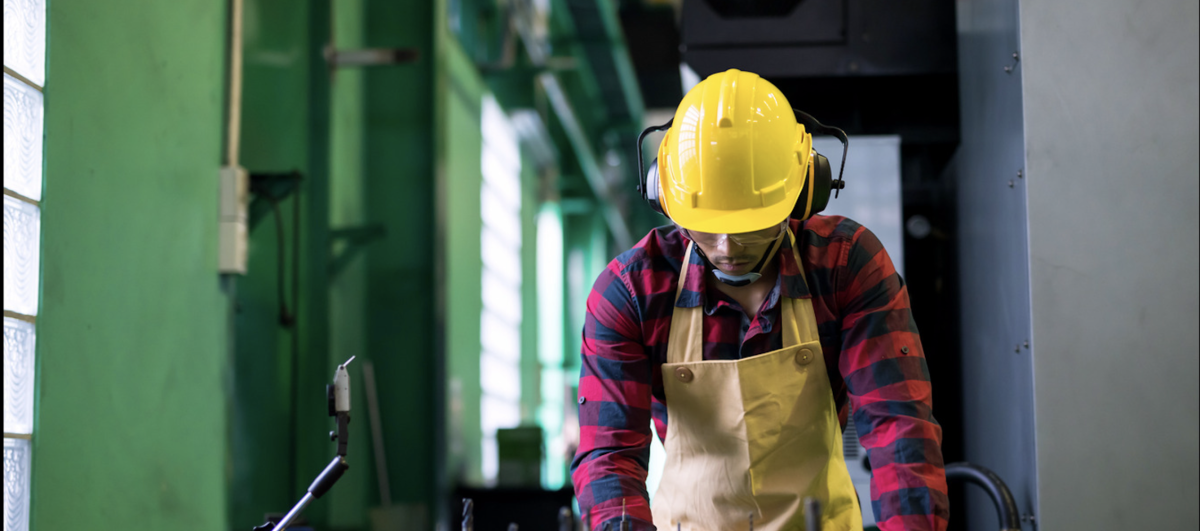
Measuring and monitoring workplace safety is crucial for any organization that values the health and well-being of its employees. However, determining the right workplace safety metrics to assess safety performance can be challenging.
While there are certain regulatory requirements around recordkeeping for injuries and incidents, organizations need to go beyond just looking at past events. The key is to utilize both leading and lagging indicators that provide insight into current safety culture and future risks. By leveraging the right key performance indicators (KPIs), businesses can gain visibility into safety issues and proactively identify opportunities for improvement.
In this blog post, we will discuss the core metrics that industrial safety leaders should be tracking. We will cover the differences between leading and lagging indicators, provide examples of commonly used KPIs, and outline best practices for implementing a safety scorecard.
Leading vs. Lagging Indicators
There are two major categories of safety metrics: leading indicators and lagging indicators. Leading indicators are proactive, preventative measures that provide insight into potential hazards before an incident occurs. Meanwhile, lagging indicators are reactive, looking backward at previous events and recordable incidents.
Leading indicators include measures such as near-miss reporting, safety training completion, safety inspections and audits. Tracking these types of metrics allows businesses to identify higher-risk areas and take corrective action to control hazards and reduce future incidents. Increased participation in voluntary safety activities like reporting near misses demonstrates a strong safety culture.
On the other hand, lagging indicators include metrics such as injuries, lost time incidents, restricted work cases, and Workers' Compensation claims. Reviewing records of past incidents and injury trends does provide valuable data to improve safety programs. However, relying solely on lagging indicators means safety issues have already impacted workers.
A comprehensive safety assessment requires a combination of leading and lagging indicators. Leading metrics drive proactive safety action, while lagging metrics provide accountability. Both are necessary for a high-performing safety management system.
Common Key Performance Indicators (KPIs)
Now let’s examine some of the most useful KPIs for evaluating workplace safety performance:
Total Recordable Incident Rate (TRIR) – Number of recordable injuries and illnesses per 100 full-time workers over a set time frame. A common lagging indicator mandated by OSHA.
Lost Time Injury Frequency Rate (LTIFR) – Number of lost time injuries per 1 million hours worked. Provides severity rate of injuries.
Days Away, Restricted, Transfer (DART) Rate – Frequency of injuries resulting in missed work, restrictions or transfers. Helps identify problem areas.
Experience Modification Rate (EMR) – Compares company’s claims history versus other businesses within anindustry. Directly impacts insurance costs.
Near Miss Frequency Rate (NMFR) – Number of near misses reported per 100 full-time employees per month. Leading indicator of safety culture.
Safety Training Completion % - Percent of required safety training completed on schedule. Proactive indicator of program effort.
Workplace Safety Inspections – Number of proactive safety inspections performed per month. Drives identification of hazards.
Corrective Actions Closed Out – Measures closeout of identified hazards and completion of corrective actions.
The KPIs tracked should align directly with the company’s safety management processes and goals. While the above metrics provide a starting point, each organization needs to tailor measures to their unique risks and strategic priorities.
Implementing a Safety Scorecard
Simply collecting data is not enough - safety metrics must be consolidated into an easy-to-use scorecard and regularly reviewed. Safety leaders should consider taking the following steps to implement an effective workplace safety scorecard:
- Identify safety metrics aligned to targets and objectives. A combination of lagging and leading indicators is recommended covering injury rates, proactive measures, risk reduction activities etc.
- Determine schedule and data sources for collecting each identified metric.
- Leverage technology such as safety management software to simplify data capture.
- Establish baseline performance for each metric based on past data and trends. Baselines create a benchmark for future measurement.
- Set metric targets to motivate continuous safety improvement across all indicators. Stretch targets help drive safety culture progression.
- Build automated reporting to publish metrics in a scorecard format on a monthly or quarterly basis.
- Make the scorecard accessible to managers across the organization.
- Review results at safety committee meetings. Analyze trends, address factors influencing metrics, and develop action plans.
- Recognize and reward positive results. Publicize improvements driven by various departments.
- Periodically reevaluate targets and KPIs selection. Adjust measures and goals based on performance.
Employing a safety scorecard standardized around established metrics allows for consistent month-to-month and year-to-year evaluation of safety outcomes. However, the process must be driven by a leadership commitment to act on the data collected. Scorecards are only effective when utilized to their full potential to inform continuous safety improvement.
Prioritizing Workplace Safety Is Imperative for Businesses
Regular assessment of both leading and lagging safety performance indicators provides businesses with the missing insight they need to reduce workplace incidents and safety risks. Safety leaders now have access to many tools to automate and simplify data collection, making the implementation of robust safety measurement strategies attainable.
The metrics highlighted in this post represent a starting point for any organization looking to enhance its safety management programs. However, companies should not limit themselves to just collecting and monitoring data. To fully leverage safety KPIs, businesses must be prepared to analyze trends, diagnose problem areas, and pursue safety excellence on all fronts – not just those mandated by regulation.
By embracing proactive indicators and addressing opportunities identified, companies can better protect their workers and their bottom lines. For customized guidance on developing an effective workplace safety scorecard, contact the experts at Northwest Safety & Risk. Our team of skilled safety consultants can partner with your organization to select meaningful KPIs, implement automated data tracking, analyze results, and support continuous safety improvement.
Don't wait for lagging indicators to show there is a problem - contact Northwest Safety & Risk today to take a proactive approach to workplace safety.